Oggigiorno, esistono tre tipi di vetro piano nel mondo: trafilatura, metodo float e calandratura. Il vetro float, che attualmente rappresenta oltre il 90% della produzione totale di vetro, è il materiale da costruzione di base per il vetro architettonico mondiale. Il processo di produzione del vetro float è stato introdotto nel 1952, stabilendo lo standard mondiale per la produzione di vetro di alta qualità. Il processo di produzione del vetro float comprende cinque fasi principali:
● ingredienti
● fusione
● formatura e rivestimento
● ricottura
● taglio e confezionamento
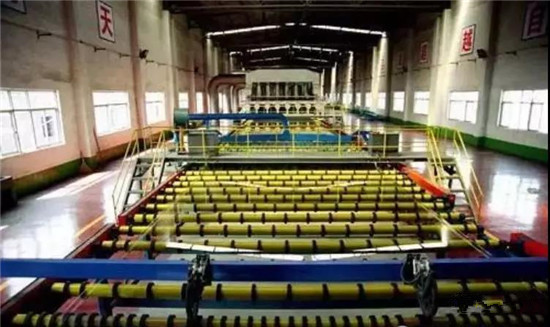
Ingredienti
Il dosaggio è la prima fase che prepara le materie prime per la fusione. Le materie prime includono sabbia, dolomite, calcare, carbonato di sodio e mirabilite, che vengono trasportate su camion o treno. Queste materie prime vengono stoccate nella sala di dosaggio. Nella sala materiali sono presenti silos, tramogge, nastri trasportatori, scivoli, depolveratori e i sistemi di controllo necessari per controllare il trasporto delle materie prime e la miscelazione dei materiali. Dal momento in cui le materie prime vengono consegnate alla sala materiali, sono in continuo movimento.
All'interno della sala di dosaggio, un lungo nastro trasportatore piatto trasporta continuamente le materie prime dai silos delle varie materie prime all'elevatore a tazze, strato per strato in ordine, per poi inviarle alla pesatrice per verificarne il peso complessivo. A questi ingredienti vengono aggiunti frammenti di vetro riciclato o resi dalla linea di produzione. Ogni lotto contiene circa il 10-30% di vetro rotto. I materiali secchi vengono aggiunti al miscelatore e miscelati nel lotto. Il lotto miscelato viene inviato dalla sala di dosaggio al silos di testa del forno per lo stoccaggio tramite il nastro trasportatore, per poi essere aggiunto al forno a una velocità controllata dall'alimentatore.

Composizione tipica del vetro
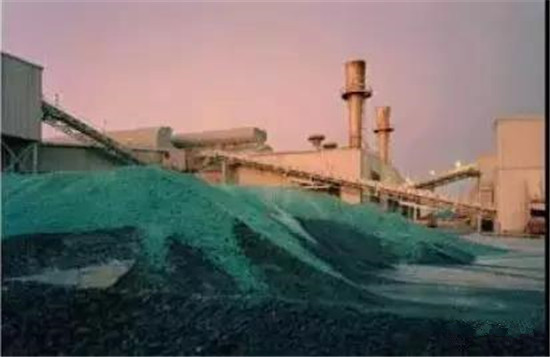
Deposito di rottami di vetro
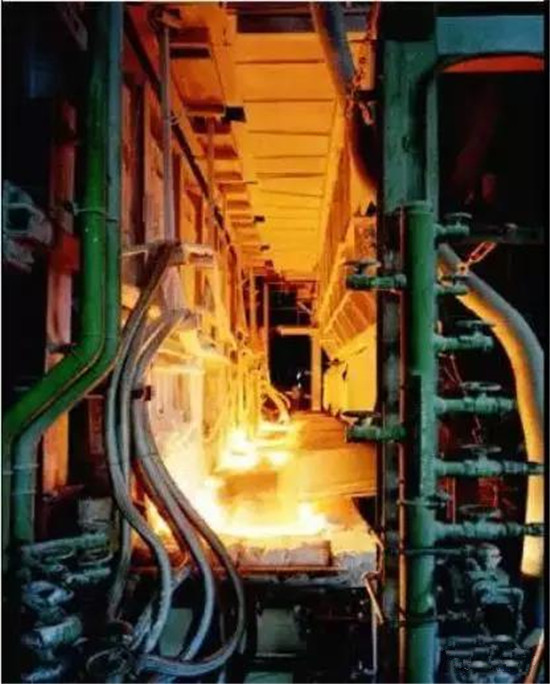
Inserire le materie prime miste nell'ingresso del forno fino a 1650 gradi tramite una tramoggia
Fusione
Un forno tipico è un forno a fiamma trasversale con sei rigeneratori, largo circa 25 metri e largo 62 metri, con una capacità produttiva giornaliera di 500 tonnellate. Le parti principali del forno sono la vasca di fusione/chiarificatore, la vasca di lavoro, il rigeneratore e il piccolo forno. Come mostrato in Figura 4, è realizzato con materiali refrattari speciali e presenta una struttura esterna in acciaio. Il lotto viene inviato alla vasca di fusione del forno tramite l'alimentatore, che viene riscaldata a 1650 °C dalla pistola a spruzzo a gas naturale.
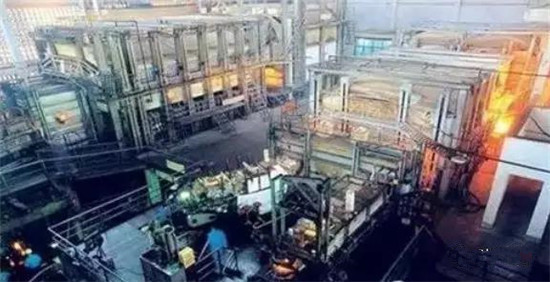
Il vetro fuso fluisce dal bagno di fusione alla zona del collo attraverso il chiarificatore e viene mescolato uniformemente. Quindi fluisce nella parte di lavorazione e si raffredda lentamente fino a circa 1100 gradi per raggiungere la corretta viscosità prima di raggiungere il bagno di stagno.
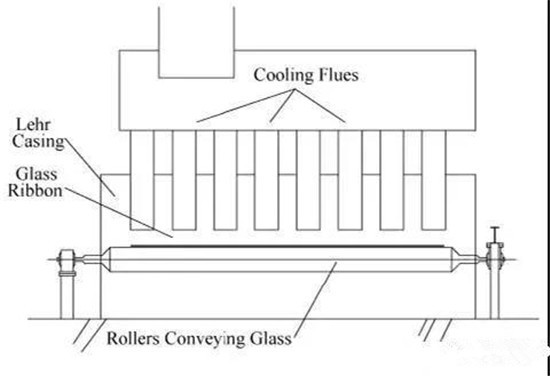
Formatura e rivestimento
Il processo di formatura del vetro liquido chiarificato in una lastra di vetro è un processo di manipolazione meccanica che segue la naturale tendenza del materiale, il cui spessore naturale è di 6,88 mm. Il vetro liquido fuoriesce dal forno attraverso la zona del canale e il suo flusso è controllato da una porta regolabile, chiamata "pistone", che si trova a circa ± 0,15 mm di profondità nel vetro liquido. Galleggia sullo stagno fuso, da cui il nome "vetro float". Vetro e stagno non reagiscono tra loro e possono essere separati; la loro reciproca resistenza molecolare rende il vetro più liscio.
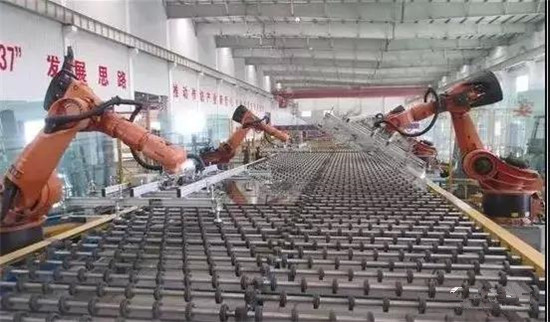
Il bagno è un'unità sigillata in atmosfera controllata di azoto e idrogeno. Comprende acciaio di supporto, gusci superiore e inferiore, refrattari, stagno e resistenze, atmosfera riducente, sensori di temperatura, un sistema di controllo di processo computerizzato, con una larghezza di circa 8 metri e una lunghezza di 60 metri, e una velocità della linea di produzione che può raggiungere i 25 metri al minuto. Il bagno di stagno contiene quasi 200 tonnellate di stagno puro, con una temperatura media di 800 °C. Quando il vetro forma uno strato sottile all'estremità dell'ingresso del bagno di stagno, viene chiamato lastra di vetro, e una serie di tiratori di bordo regolabili opera su entrambi i lati. L'operatore utilizza il programma di controllo per impostare la velocità del forno di ricottura e della macchina di trafilatura dei bordi. Lo spessore della lastra di vetro può essere compreso tra 0,55 e 25 mm. L'elemento riscaldante della parete superiore viene utilizzato per controllare la temperatura del vetro. Man mano che la lastra di vetro scorre continuamente attraverso il bagno di stagno, la sua temperatura diminuisce gradualmente, rendendo il vetro piatto e parallelo. A questo punto, acuracoat® può essere utilizzato per la placcatura in linea di pellicole riflettenti, pellicole basso emissive, pellicole per il controllo solare, pellicole fotovoltaiche e pellicole autopulenti su apparecchiature CVD per pirolisi. A questo punto, il vetro è pronto per il raffreddamento.
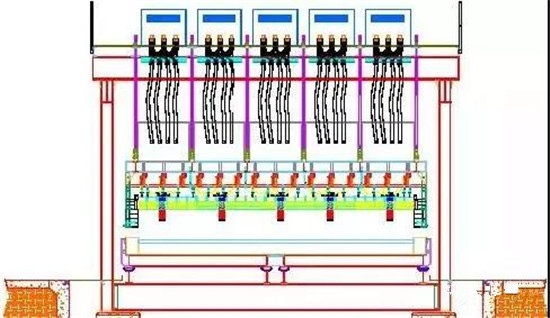
Sezione trasversale del bagno
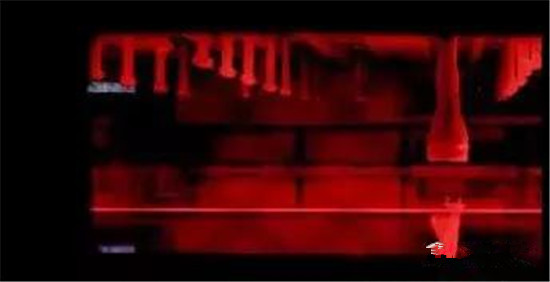
Il vetro viene steso in uno strato sottile sullo stagno fuso, tenuto separato dallo stagno e formato in una piastra
L'elemento riscaldante sospeso fornisce calore, mentre la larghezza e lo spessore del vetro sono controllati dalla velocità e dall'angolazione dell'estrattore del bordo.
Ricottura
Quando il vetro formato esce dal bagno di stagno, la temperatura del vetro è di 600 °C. Se la lastra di vetro viene raffreddata nell'atmosfera, la superficie del vetro si raffredderà più velocemente dell'interno, causando una forte compressione della superficie e dannose sollecitazioni interne alla lastra di vetro.
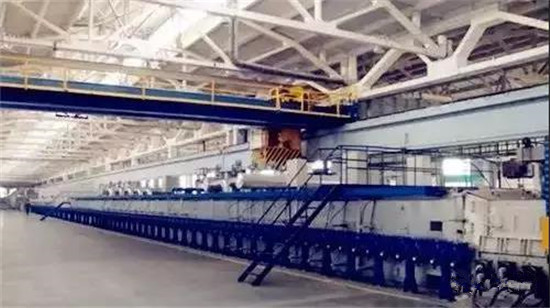
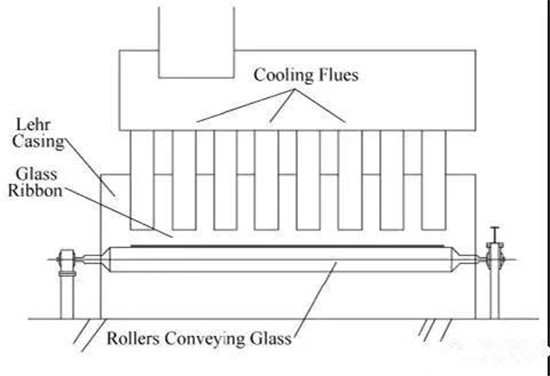
Sezione del forno di ricottura
Il processo di riscaldamento del vetro prima e dopo lo stampaggio è anche il processo di formazione di tensioni interne. Pertanto, è necessario controllare il calore per ridurre gradualmente la temperatura del vetro a quella ambiente, ovvero per effettuare la ricottura. Infatti, la ricottura viene eseguita in un forno di ricottura a gradiente di temperatura preimpostato (vedi Figura 7) largo circa 6 metri e lungo 120 metri. Il forno di ricottura include elementi riscaldanti e ventilatori a controllo elettrico per mantenere stabile la distribuzione trasversale della temperatura sulle lastre di vetro.
Il risultato del processo di ricottura è che il vetro viene raffreddato con cura a temperatura ambiente, senza sollecitazioni o stress temporanei.
Taglio e confezionamento
Le lastre di vetro raffreddate dal forno di ricottura vengono trasportate all'area di taglio tramite il tavolo a rulli collegato al sistema di azionamento del forno di ricottura. Il vetro passa attraverso il sistema di ispezione in linea per eliminare eventuali difetti e viene tagliato con una mola diamantata per rimuovere il bordo (il materiale del bordo viene riciclato come vetro rotto). Quindi viene tagliato nella dimensione richiesta dal cliente. La superficie del vetro viene cosparsa di un medium in polvere, in modo che le lastre di vetro possano essere impilate e conservate evitando che si attacchino o si graffino. Successivamente, le lastre di vetro perfette vengono divise in pile per l'imballaggio tramite macchine manuali o automatiche e trasferite al magazzino per lo stoccaggio o la spedizione ai clienti.
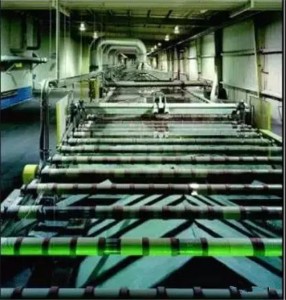
Dopo che la lastra di vetro lascia il forno di ricottura, la lastra di vetro è completamente formata e spostata nell'area di raffreddamento per continuare a ridurre la temperatura